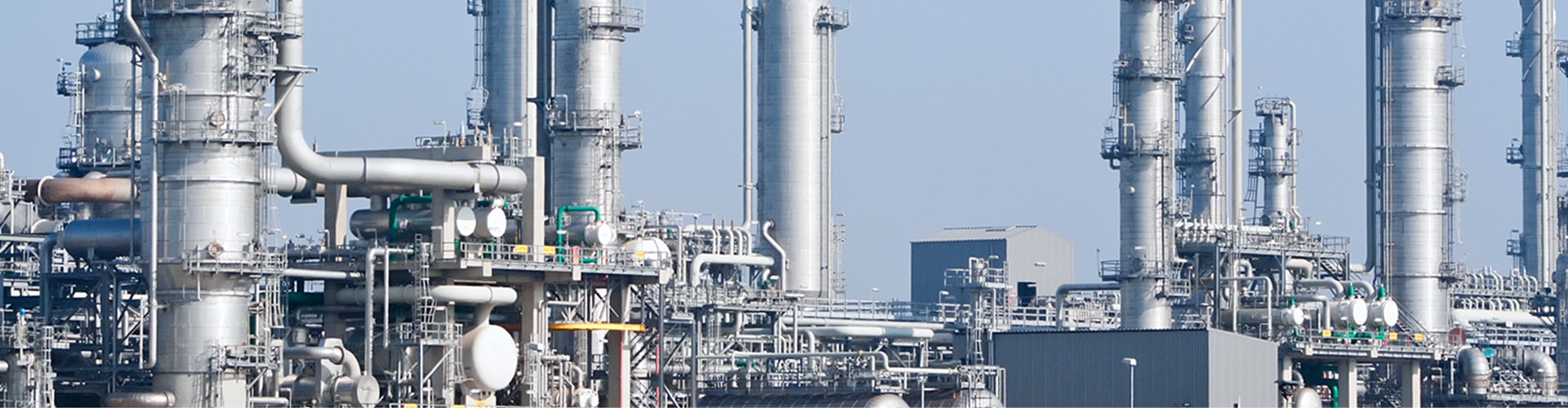
Job Openings:
Assistant Manager, Piping
Job Summary
Reporting to the Piping Manager, he/she will be responsible for reviewing piping engineering progress against approved schedule, for evaluating changes and taking corrective action when required, for providing technical guidance, and for organizing, executing and coordinating these responsibilities to ensure timely completion and meets project schedule and budget.
Duties & Responsibilities
- To check and review all work such as piping layout and information prepared by Engineers, 3D model, MTO, BQ and other deliverables of the project for compliance to project standards or specifications, applicable codes, contract requirements, quality standards and accepted engineering and construction practices.
- To assist in planning and organizing piping engineering activities and manpower requirement for the project.
- Prepare department procedures, manuals, guides, training materials and conduct training.
- To provide field engineering support/advice towards piping installation and testing at construction site.
- Performs other tasks that may be assigned or designated to him/her by his/her superior.
Requirements
- Bachelor’s degree of BS Engineering course preferably Mechanical Engineering.
- Minimum 15 years and above in the field of piping design involving detailed design, stress evaluation, production work, 3D model review, material specification and construction engineering support.
- Good knowledge of Caesar II.
- Interpretation of stress/vibration analysis report.
- Basic knowledge of AutoCAD.
- Basic knowledge of 3D model review through Naviswork or SPR.
- Ability to apply mathematical concepts in piping calculations such as exponents, logarithms, trigonometric functions, quadratic equations and other applicable formulas.
- Strong analytical and reasoning abilities.
- Good interpersonal and communication skills.
Principal Piping Engineer
As a Principal Piping Engineer, he/she shall act as key person of the project as designated by Piping Department Manager and performs the function inherent to this position. Responsible for the preparation of major piping layout, MTO sketch, and 3D CAD model review on piping system, equipment and structure, and interference detection. Has the technical responsibility for interpreting and evaluating stress/ vibration result, for reviewing piping layout, and piping information. He/She will also be responsible for reviewing piping engineering progress against approved schedule, for evaluating changes and taking corrective action when required, for providing technical guidance, and for organizing, executing and coordinating these responsibilities to ensure timely completion and meets project schedule and budget.
Duties & Responsibilities:
- To study ITB, project and design basis such as scope of work, overall project schedule, basic design data, client specification, client standard drawings, existing drawings, and plot plan.
- To assist in planning and organizing piping engineering activities and manpower requirement for the project.
- To assist in developing piping engineering and design schedule, manpower requirements, manhour distribution and execution plan based on the scope of work and approved budget manhour/schedule.
- To coordinate piping design and engineering effort with other area Lead Engineers and disciplines of the project.
- To prepare piping information list and layout and document list following standard procedure created for the project.
- To prepare piping general specification inclusive of specification for piping arrangement, piping support standards.
- To interpret and evaluate stress/vibration analysis result and provides necessary recommendation on resolving the method of analysis.
- To develop conceptual routing, piping layout and piping information of major critical equipment of the project such as tower/column, airfin coolers, heaters, compressors and reactors, preferably in 3D CAD format.
- To check and review all work such as piping layout and information prepared by Engineers, 3D model, MTO, BQ and other deliverables of the project for compliance to project standards or specifications, applicable codes, contract requirements, quality standards and accepted engineering and construction practices.
- To check and review piping material specification (line classes), specifications/requisitions for bulk and special piping components, vendor quotation evaluations and verifications of vendor documents and piping material take-off prepared by engineers for compliance to project standards or specifications, applicable codes, contract requirements, quality standards and accepted engineering and construction practices.
- To provide field engineering support/advice towards piping installation and testing at construction site.
- To perform the function inherent to Piping Key Person as designated by Piping Department Manager.
- To evaluate the performance of and provide counseling and guidance to members of the project.
- To identify and recommend training programs including cross training of piping staff within the team in collaboration with the Department Manager.
- To prepare lesson learned upon completion of the project and recommend preventive actions to avoid recurrence on future projects to Piping Design Supervisor.
- To perform other tasks that may be assigned by the Department Manager.
- To carry out engineering support work during the construction phase of the project.
Requirements:
Education:
- Bachelor Degree of any four years BS Engineering course preferably Mechanical Engineering or at least fifteen (15) years related experience and/or training; or equivalent combination of education and experience.
- Minimum of twelve (12) years in the field of piping design involving detailed design, stress evaluation, production work, 3D model review, and construction engineering support, five (5) years of which in a supervisory capacity.
Skill Requirements:
- Good Knowledge of AutoCAD.
- Basic knowledge of 3D Model review through Naviswork or SPR.
- Interpretation of stress/vibration analysis report.
- Ability to read, analyze, and interpret common technical information, contracts reports and instructions.
- Ability to respond to common inquiries or complaints from clients and ability to write effective minutes of meeting and other related business communications.
- Strong leadership qualities and analytical and reasoning abilities.
- Good interpersonal and communication.
Senior Piping Engineer (Material Specialization)
Roles and Responsibility:
- Preparation of Piping Material Specification (line classes), specifications/requisitions for bulk and special piping components, vendor quotation evaluations and verifications of vendor documents and piping material take-off prepared by engineers for compliance to project standards or specifications, applicable codes, contract requirements, quality standards and accepted engineering and construction practices.
- To calculate/validate pipe wall thickness, branch reinforcement etc.
- To prepare line index, Material summary (BM/BQ).
- To carry out engineering support work during the construction phase of the project.
- Performs other tasks that may be assigned or designated to him/her by his/her superior.
Requirements:
- Minimum of Ten (10) years in the field of piping engineering involving material, design, production work, 3D model review, stress and construction engineering support.
- Bachelor’s Degree in Mechanical Engineering or equivalent combination of education and experience.
- Good knowledge and experience of ASME, ASTM, BS and other relevant standards.
- Basic knowledge of AutoCAD/AP3D/S3D.
- Basic knowledge of 3D Model review through Navisworks or SPR.
- Strong analytical and reasoning abilities.
- Good leadership skills.
- Good interpersonal and communication skill.
Senior Piping Engineer (Stress Analysis)
Duties & Responsibilities
- Prepare, interpret and evaluate stress/vibration result.
- Review piping layout and piping information.
- Review piping engineering progress against approved schedule.
- Evaluating changes and taking corrective action when required.
- Provide technical guidance, executing and coordinating the above responsibilities to ensure timely completion and meets project schedule and budget.
- Performs other tasks that may be assigned or designated to him/her by his/her superior.
Requirements
- Bachelor’s degree in Mechanical Engineering.
- Minimum 10 years in the field of piping design involving detailed design, stress evaluation, production work, 3D model review, and construction engineering support.
- Good knowledge of Caesar II.
- Interpretation of stress/ vibration analysis report.
- Basic knowledge of AutoCAD.
- Basic knowledge of 3D model review through Naviswork or SPR.
- Strong analytical and reasoning abilities.
- Good interpersonal and communication skills.
Deputy Department Manager, Construction
Role Description (Primary)
This is a full-time role for a Deputy Construction Department Manager. The Deputy Department Manager will work closely with the Construction Department Manager, Engineering Manager and other engineering disciplines to strengthen the construction team and participate in management reviews and other administrative activities as well as project specific activities such as construction planning and cost estimation, proposal preparation, and manhour planning in the bidding and tendering phase. The Deputy Department Manager will also oversee all administrative functions including department hiring, promotions, performance appraisals, overseas assignment, and organizational changes.
Role Description (Secondary)
Responsible for overseeing all construction activities with respect to schedule, performance, procedure, and making recommendations to Project Managers for improvements and corrective actions in the project execution phase. Additionally, the role entails the overseeing of the delivery and use of materials, tools, and equipment, and the quality of construction, staff productivity, and safety. The Deputy Department Manager will also be responsible for all sites’ HSSE Management and compliance with local government and clients’ HSSE regulations.
Duties and Responsibilities
- Construction planning.
- Construction cost estimation.
- Proposal preparation.
- Manpower planning, deployment, and control.
- Coordination for resolving construction issues and managing project schedule.
- Safety mind-set and the ability to develop RA and permit to work applications.
- Written and oral communication with site workers and subcontractors
- Preparation of construction execution plan/ policies.
- Monitoring of work schedule, progress, performance, etc.
- Approving changes in specifications or procedures.
- Preparing reports, handing over procedures / closing out procedures, etc.
Qualifications
- Bachelor’s degree in Mechanical/ Construction Management engineering.
- At least 15years of experience in the field of plant engineering design and construction experience in oil & gas, petrochemical, chemical and industrial plants.
- Supervisory Skills, Construction Safety, and Construction skills.
- Ability to independently manage construction work in an operational plant (refinery).
- Good knowledge and experience in construction planning and control throughout an entire EPC project lifecycle (bidding, execution, handover).
- Possess basic understanding of QOHSE requirements.
- Proficient in MS Office & AutoCAD.
- Excellent leadership skills with ability to lead a team of multinational disciplines.
- Good interpersonal, management and decision-making skills.
- Positive attitude and result oriented.
Site Construction Manager (10 -12 months Contract)
Job Summary
This incumbent is accountable for the completion of construction work in a timely and profitable manner consistent with project objectives and within budget.
He is overall responsible to oversee all construction activities with respect to schedule, performance, procedure, and making recommendations to Project Managers for improvements and corrective actions. He is also tasked to oversee the delivery and use of materials, tools, and equipment; and the quality of construction, staff productivity, and safety. He also oversees all sites’ HSSE Management and comply to local government and client HSSE regulations.
Duties & Responsibilities:
- Supervise sub-contractor and coordinate with various agencies.
- Manpower planning, deployment and control.
- Coordinate to resolve construction issues and manage schedule.
- Safety mind-set and able to develop RA and permit to work application.
- Good written and oral communication.
- Good interpersonal skill to deal with people at construction site.
- Prepare construction execution plan/ policies.
- Monitoring work schedule, progress, performance, etc.
- Conduct meetings.
- Initiate, and coordinate meetings with other disciplines.
- Approval of change in specifications or procedures.
- Prepare reports, handing over procedures/ closing out procedures, etc.
- Responsible for all problems solving on site.
Requirements:
- Bachelor’s Degree or equivalent.
- Minimum 8 to 15 years’ of relevant experience in construction field.
- Independently manage construction work in an operational plant (refinery).
- Accountable for the completion of construction work in a timely, profitable manner.
- Experience in oil and gas or chemical projects.
- Good knowledge and experience in construction planning and execution.
Construction Engineer (1-year contract)
Objectives:
This position is accountable for preparing the detailed Construction plans in accordance with the JGCAP’s company policies as the key person under the direction by JGCAP’s Site In-charge/ Project Manager and coordinating all construction activities on site among all JGCAP’s disciplines including subcontractors using his technical experiences and construction know-how and ensuring the completion of the work on schedule.
The detail plans as described above are as follows:
- Execution formation with the direction by JGCAP’s Site In-charge/ Project Manager.
- Outline of the Construction & sequence of work.
- Temporary facilities plan (If require) and subcontracting plan.
- Manpower mobilization plan.
- Construction equipment mobilization plan.
- Work closely with the project scheduler on construction schedule and progress reporting.
- Constructability studies and plans, coordinate with Project Engineers and other related discipline as and when necessary.
- Scaffolding plan.
- Reflect the constructability plans in the inquiry for subcontracting.
- Preparation of documents such as specifications, procedures, manuals etc.
- Erection plan of extra heavy equipment, inclusive of haulage plan.
- HSSE work control plan including rules and promotion plan together with JGCAP’s Site HSSE personnel.
- Coordinate with Project team of vendor specialists for work which need vendor specialist support.
Duties & Responsibilities:
- Initiate the subcontractors sourcing, inquiry package issuing, work scope clarification, sub-contractors evaluation & selection, cost negotiation and PO issuance.
- Work scope clarification & confirmation, BQ verification and construction direct & indirect cost estimation.
- Initiate Project’s Kick off meeting with the selected subcontractor and coordinating with selected subcontractors to ensure they are in line with company or project strategies and planning. Discussing and clarifying the detail of scope of work, execution plan, commercial issue and technical issue to minimize potential future conflict.
- Carry out constructability studies, construction activities planning and execution plan for the job.
- Coordinating with all engineering disciplines to ensure design, cost and client’s requirement can be achieved.
- Handling of issued drawings or field change sheet to ensure latest drawings to be applied.
- Work closely with the team member and subcontractor to prepare all the MSRA required for the project.
- Working closely with scheduler, subcontractors and clients to plan ahead and schedule critical work paths in order to avoid delays or obstructions on mechanical completion.
- Day to day management of the site, including supervising and monitoring the work progress, site labour force and any work of subcontractors.
- Overseeing quality control and health and safety matters on site.
- Maintain knowledge on all contract terms and legal requirements for project to avoid any delay in projects.
- Identify and resolve all technical issues in Construction process.
- Liaising with clients and company project team, including attending regular meeting and submitting reports to keep them informed of progress and construction issues.
- Liaising with any vendors, consultant, supervisors, subcontractors and the general workforce involved in the project.
- Assist the JGCAP’s Site In-charge/ Project Manager to monitor and manage the overall construction cost, including subcontractors’ progress billing, construction expenses and cost of variation order.
- Prepare and submit the weekly and monthly progress/construction reports to management.
Skill Requirements:
- Degree in Mechanical engineering or equivalent.
- Over 3 years’ relevant experience in construction management field.
- Experience in oil and gas or chemical projects.
- Knowledge in construction planning.
- Knowledge and experience in sub-contracting work.
- Proficient in MS Office, MS PowerPoint and schedule reporting.
- Clear awareness of construction management tools and method of execution.
- Familiar with Construction Practices.
Senior Instrument Engineer
Job Summary
Responsible for the analysis and preparation of specifications and construction drawings, design documents for process and industrial plants in accordance with project specification schedule and customer requirements.
Duties & Responsibilities
- Responsible for field instrument and control system design work.
- Able to lead small/medium size project within budgeted MH, cost and project schedule.
- Prepare and review field instruments, Analyzer, Control Systems (DCS, ESD, F&G etc) specification, requisition, TBE, vendor document review.
- Prepare construction drawings such as Location layout, hook-up, cable routing, loop diagram etc. based on project specifications.
- Generate specification requisition for various process instruments, evaluate and select suitable instruments for required process control/monitoring application.
- Preparation of technical proposals (e.g. TBE) and cost estimation for tender projects.
- Preparation Vendor’s Document Review, BMBQ, Man-hour estimation and related.
- Engineering Support at site, attend Field Instrument & Control Inspection, FAT at vendor’s workshop and SAT & Loop Check at site.
- Perform other functions that may be assigned by superior.
Requirements
- Bachelor’s degree in Chemical Engineering, Electrical and Electronic Engineering or Instrument and Control Engineering.
- 8 years’ experience in instrument and control system design work.
- Knowledge and experience in Field Instrument Engineering as well as Control System, e.g. DCS, ESD, F&G.
- Able to work at construction site to support construction, pre-commissioning and commissioning activities.
- Good interpersonal and communication.
Lead Instrument Engineer
Job Summary
Responsible for the analysis and preparation of specifications and construction drawings, design documents for process and industrial plants in accordance with project specification schedule and customer requirements.
Duties & Responsibilities
- Responsible for field instrument and control system design work.
- Able to lead small/medium size project within budgeted MH, cost and project schedule.
- Prepare and review field instruments, Analyzer, Control Systems (DCS, ESD, F&G etc) specification, requisition, TBE, vendor document review.
- Prepare and review construction drawings such as Index, IO List, Location layout, hook-up, cable routing, loop diagram etc. based on project specifications.
- Evaluate and select suitable instruments for required process control/monitoring application.
- Lead the estimation work of BMBQ, Man-hour, technical proposal writeup, for new tender project.
- Preparation of project monthly report and attending project & client meeting as required.
- Work collaboration with other GEC and monitor daily job task assignment.
- Perform FAT/inspection for control system and field instruments as required.
- Perform SAT, Loop check, site construction and commissioning support as required.
Requirements
- Bachelor’s degree in Chemical Engineering, Electrical and Electronic Engineering or Instrument and Control Engineering.
- 15 years’ experience in instrument and control system design work.
- Knowledge and experience in Field Instrument Engineering as well as Control System, e.g. DCS, ESD, F&G.
- Able to work at construction site to support construction, pre-commissioning and commissioning activities.
- Good interpersonal and communication.
Senior Rotating/Package Engineer
Duties & Responsibilities
Lead Engineer role independently for Mechanical scope such as:
- Perform all engineering design assignment (Core: Pumps, Compressors, Blowers, Turbines, Machinery, Package Equipment. Option: Vessels, HVAC )
- Checker role for department rotating/package deliverables.
- Prepare specifications, data sheet, and inquiry documents.
- Perform all discipline engineering assignment and design work.
- Perform technical bid evaluation.
- Mechanical Handling and Movement Study.
- Coordinate with disciplines for layout.
- Review of vendor documentation and vendor management.
- Provide technical requirements and assessment for inspection and QC related matters.
- Participate in site surveys, HAZOPs, and various workshops.
- Participate in FATs, shop inspections and provide technical support during construction, pre-commissioning stage.
- Handle interface matters and coordinate with relevant parties.
- He/she must be ready to work at construction site and be ready for working overseas upon request.
- Other work related requests from Department Manager/ Supervisor.
Competencies / Preferred Skills:
- Familiar with and have experience with pumps, compressors blowers, turbines and other industrial package.
- Possess ability to interpret client requirement, identify deviations and co-ordinate for resolutions. In addition, he/she demonstrates the ability to verify own product for error free output and draft technical resolutions for issues, communicate interface matters timely to various discipline.
- Experience to lead an amalgamated team of engineers working in different locations.
- Competent in English language and proficient in MS Office programs.
- Competent in planning and coordination with relevant parties both internal and external.
Education Qualifications & Other Requirements:
- Possess a Degree in Mechanical Engineering with 12~15 Years’ experience in the industry.
- Possess on-site experience for field engineering, commissioning and troubleshooting.
- Familiar with Shell DEPs, Exxon GPs, Chevron CES and GMPs design will be an added advantage.
Senior Project Engineer
Job Summary
Responsible in providing general direction towards a successful completion of a project, ensuring the disciplines follow the quality standard set forth by the company. The job entails but not limited to identification of critical aspects of project execution and addresses them before they manifest as problems; verification and management of manhour consumption of different disciplines during the project execution.
Duties & Responsibilities
- Manage Project 3~20 million and above.
- Facilitate job interfacing with various disciplines, procurement and construction group.
- Conduct contract reviews, risk analysis and contingency plan.
- Organize proposal / project task force and staff allocation.
- Set project policy for quality, safety, cost and schedule.
- Initiate kick-off meeting with clients and internal disciplines.
- Prepare overall budget cost plan and analysis.
- Monitor and analyze project operation and schedule.
- Coordinate EPC cost estimation.
- Represent the company to client.
- Control project documents and design changes.
- Prepare project specifications and systems or processes for the execution of project.
Requirements:
- Bachelor’s degree in Mechanical Engineering, or Chemical Engineering preferred with at least 8 years of experience or equivalent.
- Have good knowledge of all disciplines, including Process Technical knowledge.
- Good Knowledge in Basic Design and P&ID.
- Knowledge of the fundamentals of project management, front-end engineering and relevant project planning and scheduling tools preferred.
- Solid track record in EPC Project Management in Oil & Gas and Petrochemical Industry.
- An effective team player with good communication and interpersonal skills, as well as strong presentation, technical, analytical and troubleshooting abilities.
- Self-motivated, with the ability to initiate plans and carry out all assignments professionally, diligently and expeditiously in accordance with established company procedures.
- Proven Leadership and Management skills.
- Proven interpersonal and relationship building skill.
Project Engineer
Job Summary
Responsible in providing general direction towards a successful completion of a project, ensuring the disciplines follow the quality standard set forth by the company. The job entails but not limited to identification of critical aspects of project execution and addresses them before they manifest as problems; verification and management of man-hour consumption of different disciplines during the project execution.
Duties & Responsibilities
- Responsible for planning, scheduling, conducting and co-ordination of the technical aspects of projects.
- To regular contact with assigned project clients to convince client along project implementation.
- To participate in client meetings and resolves project issues.
- To ensure smooth and successful execution of projects that align with project strategies and objectives through the various phases (Feasibility studies, FEED, detailed design, construction, commissioning, start-up and handover of projects).
- To ensure that projects meet safety, cost, schedule and quality standards.
Requirements:
- Bachelor’s degree preferably in Mechanical Engineering or other Engineering disciplines with 3-5 years of experience.
- Have good knowledge of all disciplines, including Process Technical knowledge.
- Good Knowledge in Basic Design and P&ID.
- Knowledge of the fundamentals of project management, front-end engineering and relevant project planning and scheduling tools preferred.
- Solid track record in EPC Project Management in Oil & Gas and Petrochemical Industry.
- An effective team player with good communication and interpersonal skills, as well as strong presentation, technical, analytical and troubleshooting abilities.
- Self-motivated, with the ability to initiate plans and carry out all assignments professionally, diligently and expeditiously in accordance with established company procedures.
- Proven Leadership and Management skills.
- Proven interpersonal and relationship building skill.
Senior Process Engineer
Job Summary
Responsible for the execution of process design involving preparation of calculations and review of process design drawings in accordance to customer specifications, applicable codes, standards and other generally accepted practices in the design of industrial plants such as petrochemical and oil refineries.
Duties & Responsibilities
- Lead a process team to carry out process design engineering work in feasibility studies, Front End Engineering Design (FEED) and detail engineering design.
- Act as Key Person to execute tender preparation, actual EPC/EPCm project execution.
- Generate project specifications, design philosophy, PFDs, P&IDs, calculations, operation manuals to comply with clients’ requirement.
- Carry out process simulations and develop heat and material balances.
- Carry out process design for reactors, columns, drums, heat exchangers, tanks and develop respective process datasheets.
- Carry out hydraulic design for pumps, compressors, blowers and develop respective process datasheets.
- Conduct and/or attend P&ID design reviews, HAZOP, IPF, SIL studies, 3D model reviews.
- Check design outputs, datasheets and drawings prepared by Process Engineers to ensure accuracy and completeness to design requirements and concepts.
- Support construction and commissioning activities at site.
- Coordinate with client, Project Team and other engineering departments and vendors.
- Monitor manhours and schedule for Process work and deliverables.
- Perform other functions that may be assigned by Department Manager.
Requirements
- Bachelor’s degree in Chemical Engineering.
- Minimum 10 years’ of experience.
Skill Requirements
- Ability to use computer equipment and peripherals to carry out routine computing tasks.
- Good knowledge in PRO/II, HYSYS, HTRI, AUTOCAD and Microsoft Office.
- Possess good communication and technical skills.
- Strong leadership qualities and analytical and reasoning abilities.
- Ability to read, analyze, and interpret common technical information, contracts reports, international codes and standards.
Senior Civil Engineer
Job Summary
Responsible for the execution of civil design involving the preparation of calculations and review of civil design drawings in accordance to customer specifications, applicable codes, standards and other generally accepted practices in the design of industrial plants such as petrochemical and oil refineries.
Duties & Responsibilities:
- To lead the Engineer team to carry out civil and structural engineering jobs in front end engineering design, detail engineering design.
- To assist discipline Manager in project civil portion manpower.
- To generate project specifications, design philosophy, calculation template to comply with clients’ requirement and local authority’s requirements.
- Civil project team manhour control, schedule control.
- To prepare foundation, structural or hydraulic calculation sheets, from simple to more complicated items, in accordance to project specifications, criteria and information. Ensuring correct and accurate calculations of loads and member sizes of structures. On average, a Civil Engineer II produces three simple foundation calculation designs a day or 1 structural calculation report a week.
- To prepare three-dimensional (3D) models and design drawings for structures and foundations as well as shop fabrication drawings.
- To supply design drawing information and instructions to Designers ensuring technical completeness and clearness of data for effective workflow.
- Usually prepares anchor bolt list and setting bolt list for client’s procurement purposes ensuring at least (+)/(-) 10% safety factor and meeting client requirements.
- Checks own design outputs and reviews design drawings to ensure accuracy and completeness to design requirements and concepts.
- May act as Assistant Key Person for small projects or NIDC projects.
- Coordinates with other Engineers and Designers to facilitate production of civil design and drawing outputs.
- Performs other functions that may be assigned by the Department Manager.
Requirements:
- Bachelor’s degree in Civil Engineering.
- Minimum of ten (10) years in the field of years plant engineering design and construction experience in Oil & Gas, Refinery, Petrochemical, Chemical, Pharmaceutical and industrial plants and consistent career experience in the engineering department
Skill Requirements:
- Ability to use computer equipment and peripherals to carry out routine computing tasks.
- Basic knowledge on STAAD, AutoCad and Micro station.
- Possess good communication and technical skills
- Strong leadership qualities and analytical and reasoning abilities.
- Ability to read, analyzes, and interprets common technical information, contract reports and instructions.
Lead Electrical Engineer
Duties & Responsibilities:
Principal
- Occasionally establishes and prepares basis of design and/or estimation and design philosophy and requirements prior to execution of electrical detailed engineering works.
- Occasionally performs electrical system studies including value engineering to determine most cost-effective design but still conforms to Client requirements.
- Normally prepares key electrical engineering documents like Key Single Line Diagrams, Conceptual Layouts, Substation Layouts and, system diagrams for Fire Alarm and Communication Systems in accordance with Client and Project requirements to facilitate the execution of electrical detailed engineering works.
- Normally prepares specifications, data sheets, requisitions, technical evaluation reports and vendor data review of major substation electrical equipment in accordance with Client and project requirements and applicable codes and standards.
- Normally establishes estimation basis and prepares technical proposals for proposal projects in accordance with Client requirements and acceptable estimation and engineering practices.
- Normally coordinates with other discipline, vendors and/or sub-contractors to ensure conformity with project and Client requirements.
- Normally acts as KP of medium to large sized standard projects, exceeding 5,000 electrical engineering manhours.
- Perform discipline project control (schedule, BM/BQ & manhour) when assigned as Project Lead Engineer.
- Assists in implementation of Department training programs by functioning as a “trainer” or “mentor”.
- Supports major phase of construction work, can assume responsibility as the Electrical Site Superintendent, Electrical QA/QC in charge, and Lead Field Engineer.
- Acts as the home base Lead Support Engineer when the major phase of the project has been shifted to site, such as purchasing of additional major equipment / material, coordinate / expedite vendors for the immediate supply of material exceptions, resolving major engineering conflicts within the approved specifications.
- Participates in site survey/ investigation of existing facilities to clarify feasibility of the design
- Participate in factory acceptance tests of electrical equipment to confirm suitability of equipment and ensure that the equipment is manufactured according to the agreed specifications.
- Performs other functions that may be assigned by superiors.
Competencies / Preferred Skills:
- Proficient in Microsoft Office Skills, AutoCAD and/or Microstation and common electrical calculation software.
- Familiar with local and international electrical codes, standards and regulations.
- Proficient in the design of electrical systems for oil/petroleum/industrial infrastructure industries.
- Familiar with ETAP and e-DPP software.
- Proficient in substation energization work.
Education Qualifications and other Requirements:
- Bachelor’s degree in Electrical Engineering.
- 15 years and above experience in electrical detailed engineering works of Oil & Gas, petrochemical and other related industrial plants, including five (5) or more years in frontend engineering and proposal / estimation works and additional five (5) or more years infield engineering works.
Email us:
If you would like to apply for the listed job position, please submit your resume giving full career details via email to recruit.jsgp@jgc.com
Only shortlisted candidates will be contacted.